Swiss-style CNC Turning
Revolutionary Machining
Swiss-style CNC turning machines, also known as Swiss lathes or Swiss screw machines, originated in the 19th century to create the tiny, intricate parts needed by the Swiss watchmaking industry. They have evolved into extraordinary, technologically advanced machines.
Modern Swiss-style CNC turning machines take precision manufacturing to a new level. Their revolutionary capabilities offer significant advantages in the production of small, complex, tight-tolerance parts. They can handle some of the toughest manufacturing challenges for very small diameter components.
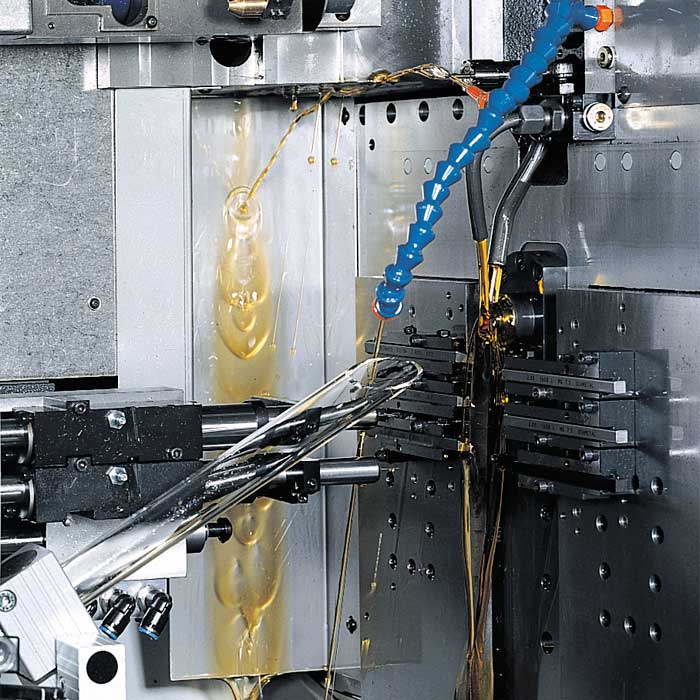
Unique Features
- Sliding headstock – This distinguishing feature allows bar stock to turn while moving back and forth along the Z-axis.
- Guide bushing – An integral component of Swiss-style CNC turning machines, this device firmly supports the bar stock.
- Proximity of material to cutting tools -- Only the portion of the bar stock being machined advances into the tooling operations area.
- High number of axes – Merit’s Swiss-style CNC machines have up to 11-axes which dramatically increases manufacturing capabilities.
- Live tooling – This feature increases the machines’ functionality, including allowing multiple tools to be used simultaneously.
- Oil as cutting fluid – Merit’s use of oil rather than water-based coolants in the operation of these machines proves to be cost-efficient and eco-friendly.
- Small diameter capability – Ideal for manufacturing premium quality components ranging from 0.3mm to 38mm in diameter.
Benefits
- Superior stability and precision is maintained throughout the machining process.
- The unique ability to move along the Z-axis allows these machines to produce part designs other machines can’t handle.
- Tight tolerances are readily achievable, even on parts with complex geometrical designs. This is due to the unique configuration of the sliding headstock and guide bushing.
- Machining occurs very near the guide bushing which minimizes deflection and vibrations within the bar stock, even with longer material. This translates to an exceptional degree of accuracy. Heavy cuts can be made without sacrificing the precise dimensions of a part. It also makes the machines ideal for producing cylindrical parts, including long parts with small diameters.
- Typically all cutting can be done in a single pass without the need for backtracking.
- Multiple operations can be performed at the same time, streamlining production. These include: drilling, tapping, milling, turning, knurling, threading and broaching. This often translates to parts being completed in a single cycle, rather than requiring the need for multiple machines and operations.
- Easily handles complex part designs, including those with thin walls or intricate features.
- All of Merit’s Swiss-style CNC turning machines are fitted with automatic bar feeders, minimizing downtime and increasing production.
- Utilizing oil as a cutting fluid has key advantages over water-based coolants. Oil does not rust, which enhances machine longevity and reduces the need for costly repairs. Water-based coolants are prone to bacterial growth and foul smells. They can also be very irritating to workers’ skin.
- Merit takes the added step of recycling 100% of its oil. Our unique, custom-built system for this process results in significant cost savings as well as being better for the environment.
- The same benefits hold true for the mineral spirits used when washing parts. We also recycle 100% of those solvents in our on-site system.
For more information on our Swiss-style CNC Turning capabilities, please contact us